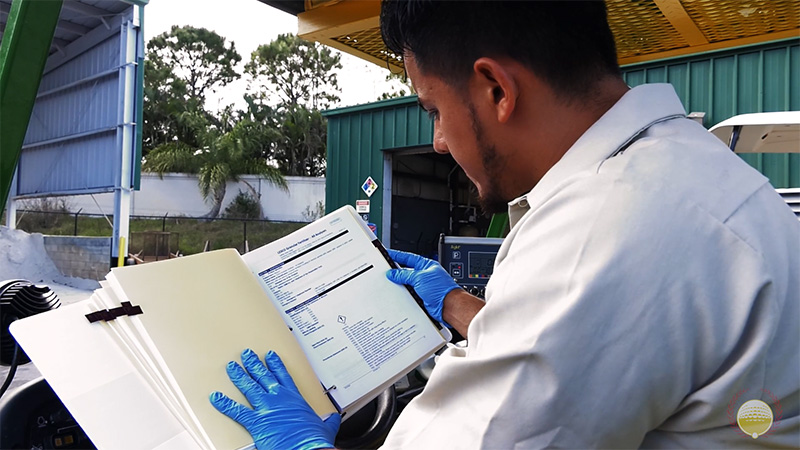
Safety plans and SDSs are critical parts of an effective safety program. Photos courtesy of Golf Safety
Editor’s note: The following article was supplied by Golf Safety. All product claims, research cited and other information is directly from the company.
If anybody understands just how many moving parts there are when running a golf course, it’s Golf Safety. Having worked with golf courses across America to help crews
avoid OSHA violations and liabilities for over 20 years, our team has seen our share of safety mistakes.
We’ve got bad news and good news. The bad news is you’re probably making a few of these mistakes. The good news is that Golf Safety has compiled the 10 most common
OSHA violations we’ve encountered over the years in this list so that you can fix them. Run through this list carefully to see if you’re guilty of any (or all) of these violations, and you can avoid crew injuries and OSHA fines!
1. Written Safety Plans
The most common safety mistake golf course superintendents make is not having written policies on all potential safety issues. OSHA requires written safety plans/policies on dozens of topics. The most common written safety plans required by OSHA are:
A hazard communication program. This written plan concerns the communication of the hazards that chemicals present to your crew and their “Right to Know.” It is the responsibility of golf course management and individual crew members to handle chemicals safely, understand
chemical labels, and understand the Safety Data Sheets (SDS). Every crew member should be familiar with your “HazCom” plan. Crew members should be trained on it as soon as they are employed and then annually as the plan is updated. The
steepest and most frequent OSHA fines usually come from an insufficient or absent Hazard Communication Program.
A Personal Protective Equipment (PPE) program. After identifying the potential hazards on your golf course, superintendents should create a written plan for equipping each crew member with the necessary PPE for their tasks. Superintendents are responsible for making sure that crew members have their
PPE selection for each task explained to them. This plan should also involve the selection of PPE that is correctly fitted to each crew member.
A respirator program. If any tasks on your golf course require the use of a respirator, you are required to have a written respirator program. This program must outline how the respirator is used. It must include proof that crew members who use respirators are trained. The
program should also outline the necessity, frequency, and process of respirator fit tests.
A lock out/tag out program. Your course contains electrically powered equipment, electrical systems, and machinery powered by mechanical, hydraulic, pneumatic, chemical, electrical, thermal, or other energy sources. OSHA requires a Lock Out/Tag Out program for these. This plan should
provide written procedures for the isolation of this equipment. All of these systems need to be isolated before work begins.
A heat illness prevention plan. Previously in California only, but now becoming nationwide, superintendents are required to take steps to prevent heat illness. Management must draft a written document to encourage implementation. This program needs to cover crew and management training,
providing water and adequate shade to crew members, and the symptoms and warning signs of heat illness.
A bloodborne pathogen program. One of the most common injuries in all industries involve blood. Your crew, including the janitorial staff, must have a written manual for what to do if someone starts bleeding or they get involved in a first aid situation which involves bodily fluids
like CPR. This written plan must be accompanied by yearly hands-on first aid training.
An emergency plan. Though they will hopefully never happen, your crew needs a written guideline on what to do in case of emergencies. The Department of Environmental Protection requires that you have a written Spill Control and Countermeasure Plan. In contrast, OSHA requires
an Emergency Action Plan, and Fire Rescue needs a fire hazard Pre-Plan. All emergency plans should lay out precisely what protocol is in place in the case of a spill, leak, fire, or other emergencies. The plans should detail the procedures the crew
should take in the event of an emergency, as well as the resources available to them specific to your golf course.
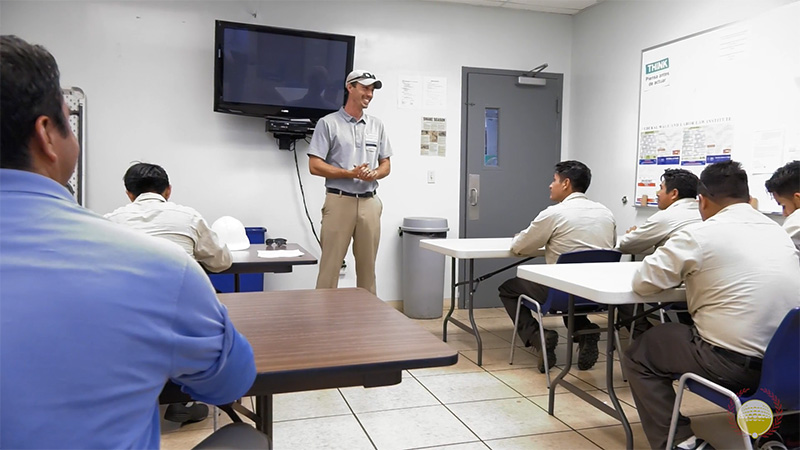
Safety training should happen regularly, and taking attendance is important.
2. Safety training
The second most common and frequently penalized safety deficiency in golf course maintenance is a lack of frequent safety training. OSHA has thousands of regulations about safety training that cover hundreds of topics. Monthly safety trainings will make
you much more likely to be compliant when the OSHA inspector arrives. To prove you’ve done training, document who is in attendance, what subjects were covered, and your crew’s proof of understanding. You can show this proof of knowledge
through tests, quizzes, or worksheets. Golf Safety training services include instructor's guides, quizzes, answer sheets and attendance sheets.
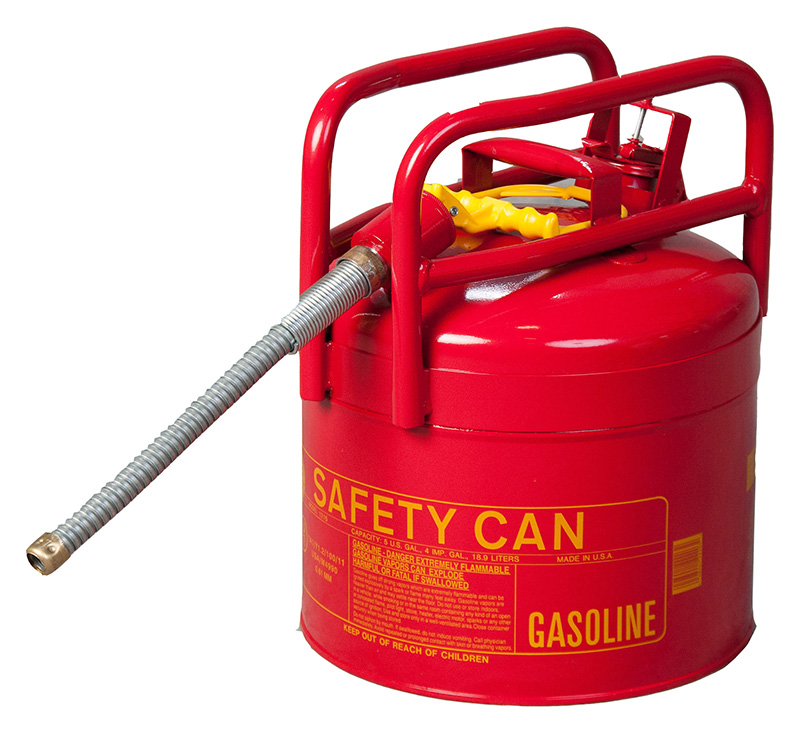
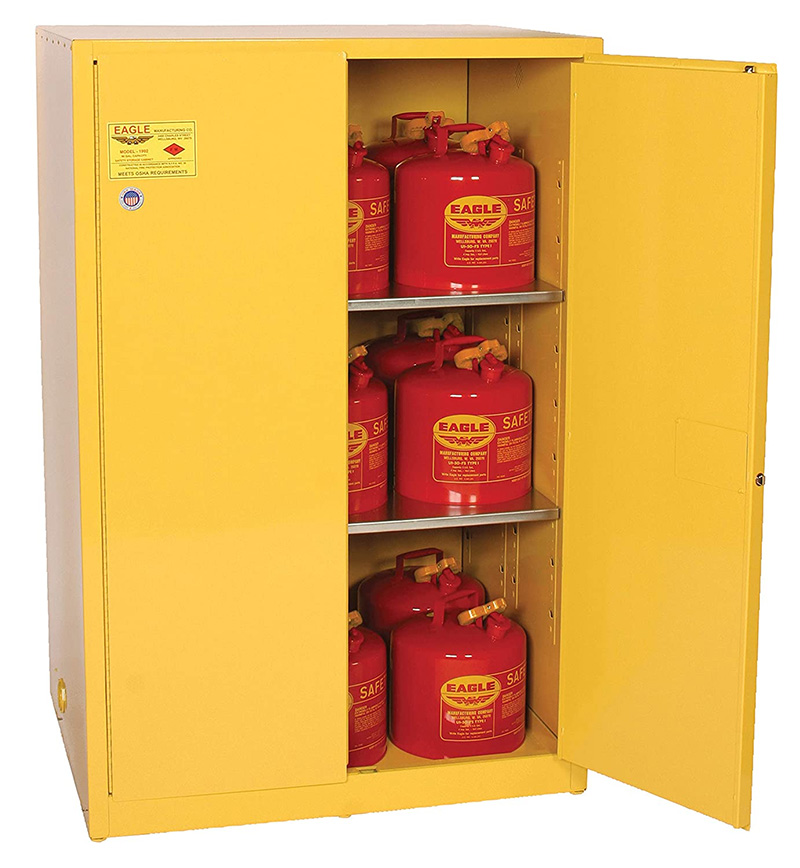
Type II safety cans and a flammable cabinet
3. Fuel can storage
Make sure you’re using the correct type of fuel cans to transport and store fuel on your golf course. Only approved containers and portable tanks may be used for flammable liquids. Plastic cans are unsuited to flammable liquids, so type I and type
II safety cans need to be used. As per OSHA regulations, you may store no more than 25 gallons of flammable liquid in a room outside of an approved storage cabinet. Don’t make the mistake of thinking that, because you have safety cans, you don’t
need a flammable cabinet. Under OSHA regulations, you may need both to store flammable liquids safely.
4. Pesticide storage
Pesticides are poison. Therefore, you have to follow proper procedures when storing them. A poorly managed pesticide storage area is unsecured to the public, has a dirty floor and wooden shelves, and has no sprayer filling area, signage, eyewash, or safety
shower. Proper pesticide storage protocols include secondary containment, a sealed floor, triple containment for the most dangerous substances, and metal shelving. Keeping your eyewash stations and safety showers adequately maintained is essential
to ensuring risk management around pesticides.
5. Rinsate recovery
Improper handling of the pesticide rinsate is a significant mistake that superintendents can make. It is imperative to ensure that you have a system in place that will recover any trace amounts of pesticide spilled in the mix/load process along with the
possibility of a significant spill during the process. Rinsate becomes a waste problem when it cannot be recycled or reused on the golf course at or below label rates. Your spray equipment and rinsate recovery equipment requires periodic cleaning
to keep its components in good working condition especially when switching from one pesticide to another. Improper management of rinsate has the potential to contaminate surface and groundwater. Do not store rinsate unless you have a plan for its
disposal. If you are recovering it and plan to apply it back to the golf course, make sure you have filters in place to remove any debris from the rinsate before putting it back into sprayers.
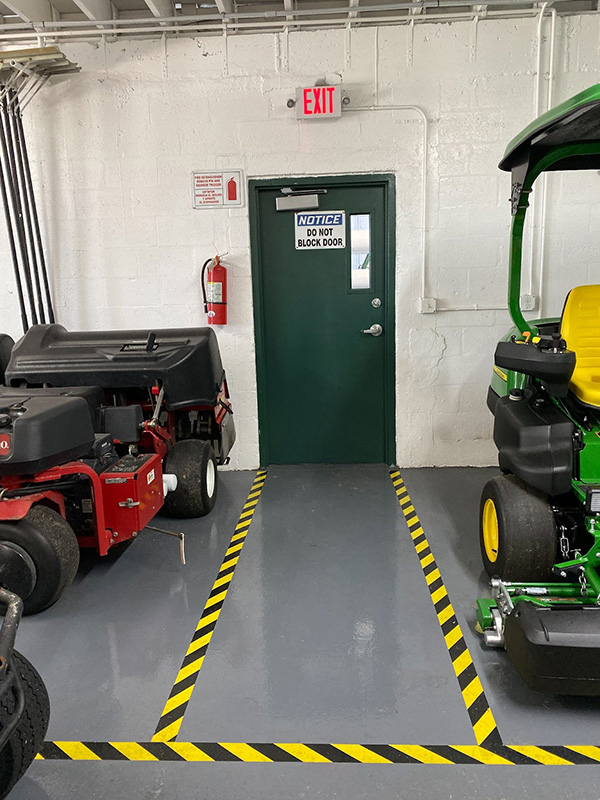
There should be a clear path connecting your emergency exits.
6. Emergency exits
When most people look at a maintenance facility with its large bay doors fully open, they would think that they have no issue with “Emergency Exits” but unfortunately these “garage or bay” doors are not technically emergency exits.
These doors take too much time to open in an emergency, and are often blocked by mowers and tractors. OSHA or Fire Rescue inspectors want to see a clear aisleway connecting your emergency exits, like in the photo above.
7. Equipment wash pads
The water that comes off any equipment wash is classified as “industrial waste.” That includes wash water from golf maintenance machinery! You can’t dump any of this water without a permit. You also can’t let wash water drain into
storm drains, bodies of water, or septic tanks. The solution is investing in a wash pad, from which you can recycle your wash water or discharge it into a designated sanitary sewer system.
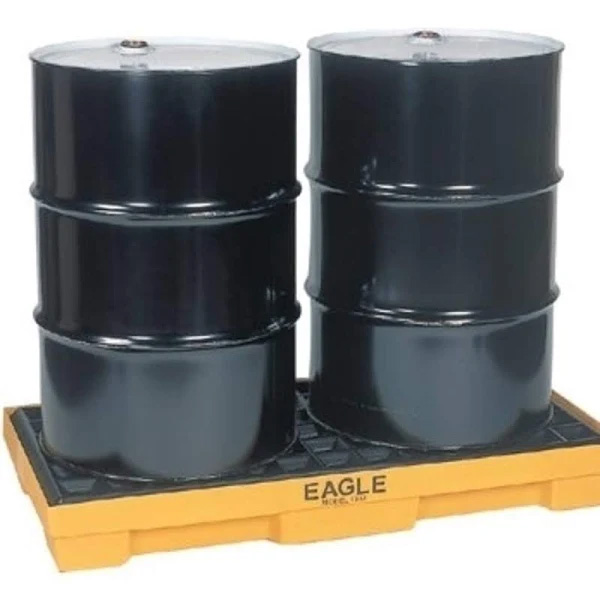
Secondary Containment Pallet.
8. Motor oil storage
Motor oil and other lubricants must be stored properly to minimize the risk of spills and the environmental damage they can cause. All drums and containers should be checked for leaks and damaged ones should be appropriately disposed of. The oil must
be labeled appropriately, so the contents of the drums are visible. Depending on the total quantity of petroleum products you store (gas, oil, diesel, etc.) some type of secondary containment is probably required. This can range from an inexpensive
secondary containment pallet (photo above) to more elaborate concrete slab-type oil storage areas.
9. Compressed air lines
If your compressed air lines are made of PVC, it’s time to make a change. PVC compressed air lines are prohibited by OSHA, and prone to shattering. If you need to make the switch in stages, make sure to start with those at eye level, as that’s
the most dangerous place a crack could occur. Proper air lines can be made of type L copper, aluminum piping, or galvanized piping as alternatives to PVC.
10. Improper use of extension cords and receptacles
Those incredibly useful multiplugs you’re using everywhere might present significant fire hazards. They are designed for low electrical loads, like computers and chargers, not for appliances such as refrigerators and microwaves. They’re
especially not meant for use with shop equipment like grinders and saws. Larger equipment will often exceed the ampere rating limit on a plug strip. If you’re using a flexible extension cord, OSHA indicates that it may not be routed through
walls, windows, ceilings, floors, or similar openings. Extension cords should not be used as permanent wiring.
This list, though extensive, only covers a few of the easy-to-miss OSHA violations that happen in golf maintenance operations. The list of potential mishaps is long, and we at Golf Safety know your time as a superintendent is limited. That’s why we have partnered with GCSAA to offer their members a 10% discount on our services! Golf Safety will send a team member to your facility to assess the safety hazards specific to your golf course and create comprehensive, detailed safety plans and SDS plans to keep you OSHA compliant. We also offer safety training videos in both English and Spanish
to help keep your crew informed, as well as attendance and quiz systems. We’re excited to take your safety compliance worries off your hands and let you get down to business!
Schedule a demo with Golf Safety today to find out how their services can help you.