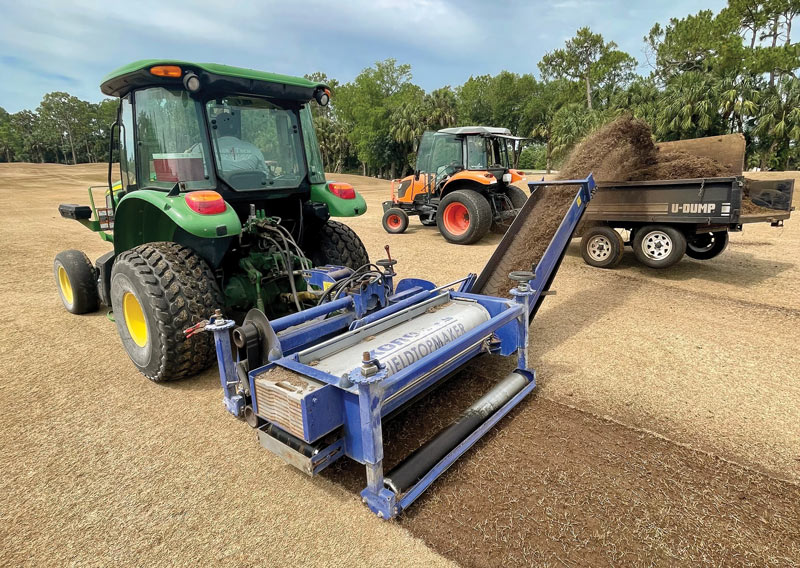
The renovation of Olde Florida Golf Club in Naples, Fla., involved some traditional heavy lifting — extensive regrassing, brand-new bunkers — as well as some strategic letting-be. Here, a fairway gets fraise-mowed to eliminate undesirable bermudagrass varieties before the fairway is regrassed with TifTuf bermudagrass. Photo by Darren Davis
By now, there’s a good chance Darren Davis has gone fishing. The Certified Golf Course Superintendent at Olde Florida Golf Club in Naples, Fla., has also perhaps walked on the beach. But for six months this year — from April through September — Davis basically lived at the club where he has tended turf for more than 29 years.
That’s because Olde Florida underwent its most extensive renovation since it opened in 1993. And Davis, who knows the course’s nuances like nobody else, was the person in charge of the $4.5 million renovation, which was done primarily to improve playability and aesthetics. Olde Florida reopened Nov. 1.
“It was a long summer,” Davis, a 32-year GCSAA member who served as president of the association in 2018, said in September as the renovation was winding down.
But while the summer was long and tiring for Davis, it was also gratifying. “(The renovation) has absolutely rejuvenated me,” he says.
Inside information
Davis was hired as Olde Florida’s construction superintendent in 1992 and was actively involved in the course’s construction, grassing and grow-in. He is the only superintendent the club has ever had. “Managing it this long has given me a unique perspective on all of the course’s subtle intricacies,” Davis says.
The renovation’s price tag, which also included updating the driving range, would’ve been higher if not for Davis’ experience. He knew where he could save the club money.
Consider the bunker redo, which made up $890,000 of the renovation’s total price. The existing sand from the front nine bunkers — about 149,000 square feet at an average depth of 6 inches — was removed, stockpiled and kept clean. Most of it was later used on the fourth and eighth fairways as well as on smaller areas on the sixth and seventh holes to modify the soil and improve drainage. Davis knew exactly what to do with it.
Editor’s note: An Illinois superintendent repurposed old bunker sand as a growing medium for native wildflowers and grasses, creating valuable habitat for insects and small animals. Read more in A new use for old bunker sand.
While Leibold Irrigation’s construction division was selected as builder of the project, Davis oversaw all material purchases to avoid the normal markups that contractors charge for securing such materials.
“The club has confidence in me as a 29-year employee and a Certified Golf Course Superintendent, and knew I was able and willing to track expenditures and be accountable for them,” Davis says.
Regarding Leibold Irrigation, Davis says he selected the company because it fit his vision for the project. He calls Leibold a “boutique” firm because, he says, the company fully invests itself in its projects and doesn’t spread itself too thin by taking on too many projects at once.
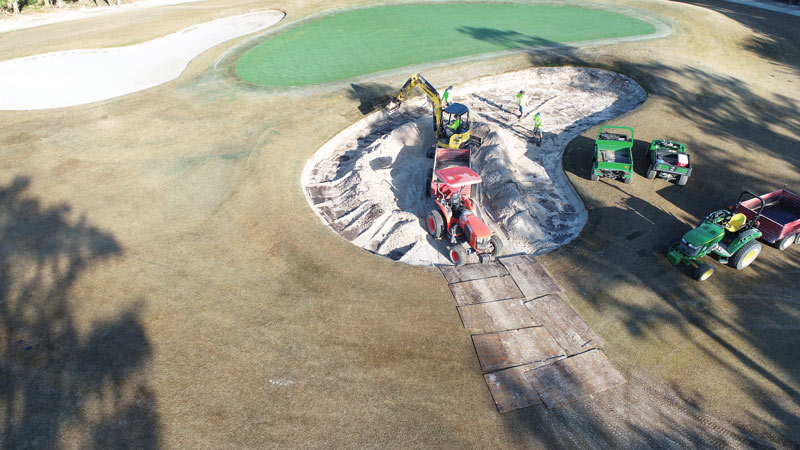
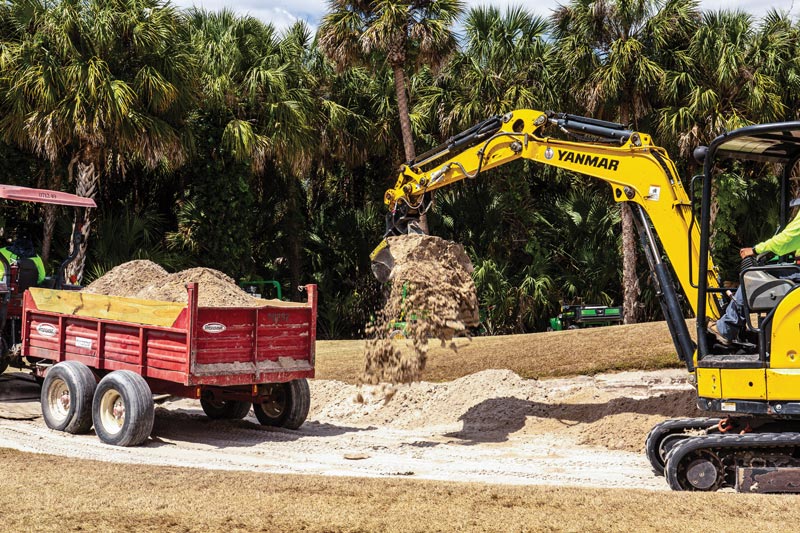
Almost 20% of the budget for the renovation project at Olde Florida went toward bunkers, which hadn’t been updated since their original construction 1992. Improvements included installation of new drainage. Photos by Darren Davis
John Leibold, founder and president of the East Dubuque, Ill.-based outfit, says he was impressed with Davis’ meticulous approach to the project. “The thing about Darren is that he plans as good as anyone. He does his homework ... and then some,” Leibold says.
Another key confidante on the project was golf course architect Greg Muirhead, the senior vice president of Rees Jones Inc., the firm that designed Olde Florida. Muirhead was on the property with Davis when the course was built.
“We were both very young and probably thought we knew a lot more than we did back then,” Muirhead says. “But Darren has always been extremely passionate about whatever it is he’s involved in. That kind of passion is hard to find, but he has maintained it for almost 30 years at Olde Florida.”
Things are ‘popping’ again
The renovation touched most areas of the golf course and included a regrassing. It did not include a greens renovation, however (more on that later).
While the bunker renovation took about 20% of the project’s total budget, Davis believes the club will get a solid return on its investment, especially given that it’s the first time the bunkers have been renovated. Over the years, the bunkers had slowly lost some of their original shaping from normal wear and deterioration, particularly in their fingers.
The bunkers were also originally built without liners. Today, bunker liners are a mainstay in the industry, and there are several bunker construction methods to choose from that weren’t available in 1992. After careful research, Davis chose Better Billy Bunker because he thought the company’s technique could combat South Florida’s sometimes-torrential rains and keep the bunkers from washing out, among other things.
“There have been many days in the summer when all of our 16 crew members would spend eight hours doing nothing but pumping water out of the bunkers and re-raking the sand,” Davis says, noting that now the bunkers can withstand an inch of rain in an hour, and playability and aesthetics won’t be affected.
Editor’s note: Read more about bunker drainage and liners in Renovating golf course bunkers: 7 key considerations.
Tom Wildenhaus, Olde Florida’s director of golf, has been on the property for as long as Davis and says the bunkers have regained their contour and definition. “I remember what they looked like when the course opened — they just popped,” Wildenhaus says. “Now when I drive through the course, they’re popping again.”
The turf is also popping, thanks to being regrassed with TifTuf bermudagrass. The course’s tees, fairways, roughs and approaches, which were originally seeded with Tifway 419 bermudagrass, had been overrun with several other varieties, including common bermudagrass.
“We’ve known for the last 15 years that we had numerous varieties of bermudagrass that existed on the property,” Davis says. “We did a good job of managing them, though.”
But TifTuf is a cut above. While Davis is impressed with the number of new bermudagrass varieties that have been developed in the past 20 years by different universities, he recommended the club select TifTuf for several reasons, including its drought tolerance, upright growth habit and improved shade tolerance.
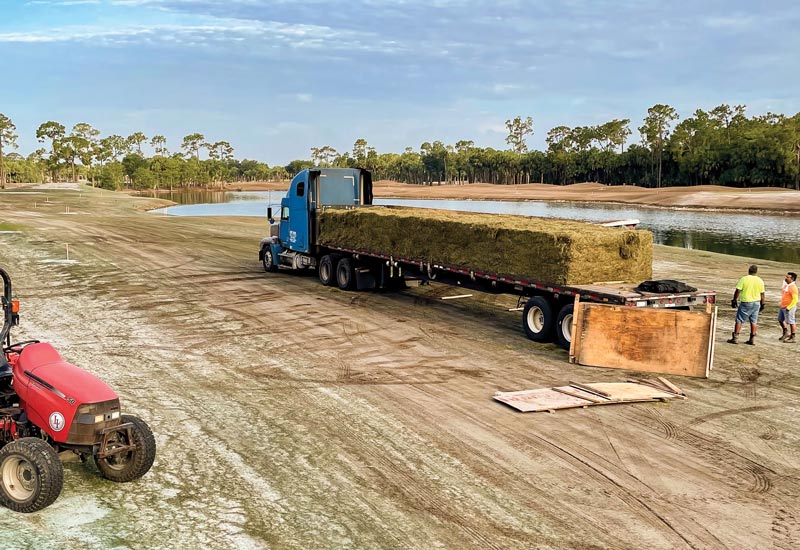
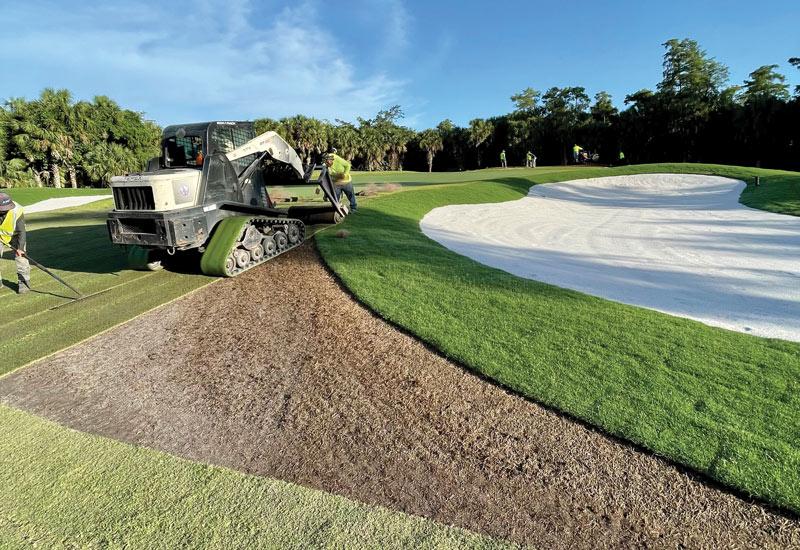
Aside from greens, all of Olde Florida’s surfaces were regrassed in 2021. Approximately half of the 112 acres were sprigged (top), and the remaining acres were sodded. Photos by Darren Davis
From a playability standpoint, Davis says TifTuf will win over Olde Florida’s members. He explains that the hybrid, which features 27 chromosomes, grows upright with a fine leaf blade. “It almost looks like a cool-season grass, like ryegrass,” adds Davis, who has been trialing the variety on plots at Olde Florida for three years. “It also recovers better than other varieties.”
Coincidentally, Wayne Hanna, Ph.D., the decorated turfgrass scientist at the University of Georgia, began development on TifTuf the same year that crews broke ground on the construction of Olde Florida. Davis consulted Hanna and other agronomists and university researchers about TifTuf, and they all endorsed it.
Wildenhaus believes the club’s members will embrace the variety. “As this grass matures, I think the ball will really sit up nicely,” he says. “The look of it is wonderful.”
Growing turf to eradicate it
Before the TifTuf regrassing, Davis had to rid the course of all of those bermudagrass varieties, and he knew he needed to kill about 99% of the previous varieties for the regrassing to be successful. It was a tall task, considering bermudagrass is difficult to kill, but he had several weapons at his disposal.
The eradication began in March when the club was still open for play and included three glyphosate applications about one month apart. Knowing that bermudagrass needs to be actively growing to be eradicated, Davis and his crew fertilized and irrigated it throughout the process. In essence, he needed to get the grass growing so it could be killed efficiently.
Davis also learned from research by turfgrass scientists Mike Richardson, Ph.D., from the University of Arkansas, and Jim Brosnan, Ph.D., from the University of Tennessee, that fraise mowing — a cultivation practice that physically removes large quantities of a turfgrass sward (thatch, organic matter, soil, etc.) — could enhance eradication of existing bermudagrass when combined with herbicide applications.
“Bermudagrass is so hard to kill because it has millions of growing points — above ground, below ground and at ground level,” Richardson says. “The stolons, crowns and rhizomes can be 7 or 8 inches below the surface, and just getting enough herbicide down there to kill it is oftentimes a challenge. Our theory is to use fraise mowing to remove as many of the growing points as possible (before spraying herbicide). Then there are fewer stolons, crowns and rhizomes, so the bermudagrass becomes easier to kill.”
Watch: Darren Davis discusses why he added fraise mowing as a step in Olde Florida’s overhaul:
Davis consulted Richardson several times about fraise mowing before implementing the practice about 10 days after the second glyphosate application. Davis and his crew fraise-mowed the centers of each hole, removing about 1.5 inches of material from about 50 of the course’s 112 acres.
For Davis, there was no other way to approach the eradication, which took four months. “We would have wasted a lot of time and money if we didn’t achieve a high level of eradication,” he says.
Putting surface satisfaction
Although it was the biggest renovation in Olde Florida’s history, the club’s greens weren’t a part of it. The USGA-style greens were resurfaced about 21 years ago with TifEagle bermudagrass and remain in excellent condition, Davis says, noting that a recent physical analysis of the greens mix, choker layer and gravel layer revealed that a greens renovation wasn’t necessary.
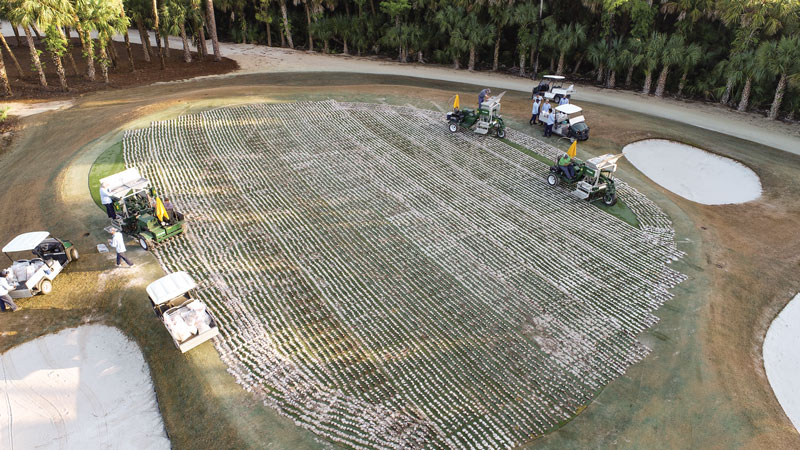
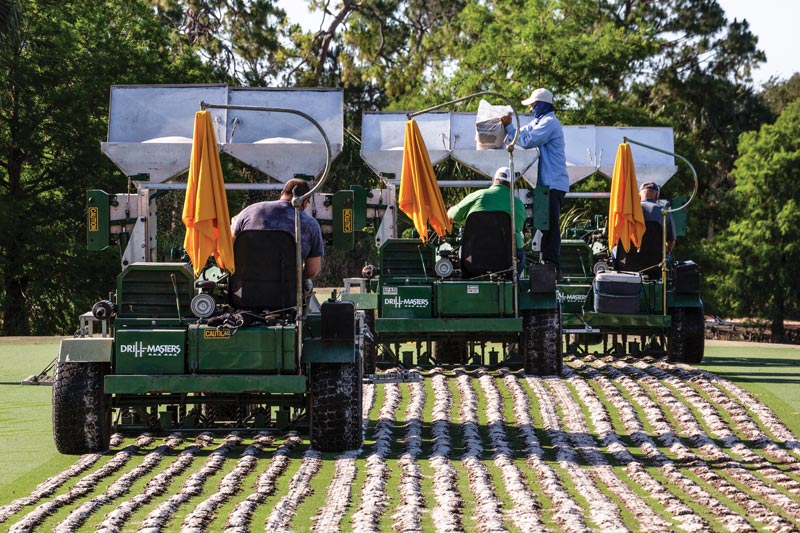
Cultural practices such as drill-and-fill aerification have helped sustain the health and quality of Olde Florida’s putting surfaces, which kept them off the renovation to-do list. The greens construction is 29 years old; the TifEagle bermudagrass on the greens is 21 years old. Photos courtesy of EPIC Creative
Davis says the saturated hydraulic conductivity could be improved, but it’s not yet at a level that’s detrimental to the turf. He maintains that consistent and aggressive cultural practices over the past 21 years — aeration, vertical mowing, topdressing and appropriate fertilization — have enabled the greens to stay healthy. Davis says the course’s greens are still 99.9% pure TifEagle.
Another reason the greens weren’t renovated is that it would have added about $1 million to the renovation’s price tag. “It was money that didn’t need to be spent,” Davis says. “Why spend $1 million on something that didn’t need to be done? I’m a superintendent who treats every dollar of the club’s money as if it’s my own money.”
Watch: Get an up-close look at the drill-and-fill process on Olde Florida’s greens, and hear from superintendent Darren Davis on the practice’s objectives:
The course’s irrigation system didn’t require a complete redesign — the original system was designed with excellent individual head-to-head coverage, Davis says — but those controlled heads were updated to catch up with current technology. Specifically, the “critical components” of the new heads can now be easily accessed for maintenance by simply removing three screws on the top of the head. “On the previous irrigation heads, this would have required us to dig up the head,” Davis says.
The irrigation system’s field satellites were also replaced. “The technology has come so far in the last 11 years that it warranted the replacement of the field satellites,” says Davis, who negotiated the sale of the old irrigation heads and satellites to a company in Arizona that buys used irrigation components for refurbishing and reselling.
Davis says there were “countless ancillary projects” that were also completed during the renovation. For instance, several trees were removed on the slope of the mounds to the left of the landing area on hole No. 1, and the area was reshaped to provide better playability on holes 1 and 10.
Show and tell
Another reason the Olde Florida project went smoothly — and it’s a big one — is Davis’ focus on maintaining clear lines of communication with members. He created a blog when the project began and posted to it regularly, complete with photos and explanations about certain procedures. Davis also offered members guided tours of the golf course during the renovation.

GCSAA Past President Darren Davis, CGCS, has led maintenance at Olde Florida Golf Club since it opened in 1993. Photo courtesy of EPIC Creative
“Showing them what we were doing ... you could see the excitement in their faces,” says Davis, who holds a bachelor’s degree in communications from Florida Gulf Coast University in addition to his certificate in turf management from Penn State University.
Davis’ communication skills are directly related to the passion he has for Olde Florida, which is still burning strong after 29 years.
“It would be easy for someone like Darren, who has been at the club for so long, to get complacent, but he’s not like that at all,” Richardson says. “He’s always looking at ways to improve on what’s he doing.”
And Davis will continue that approach, even after the biggest renovation in Olde Florida’s history.
Lawrence Aylward is a freelance writer from Medina, Ohio.