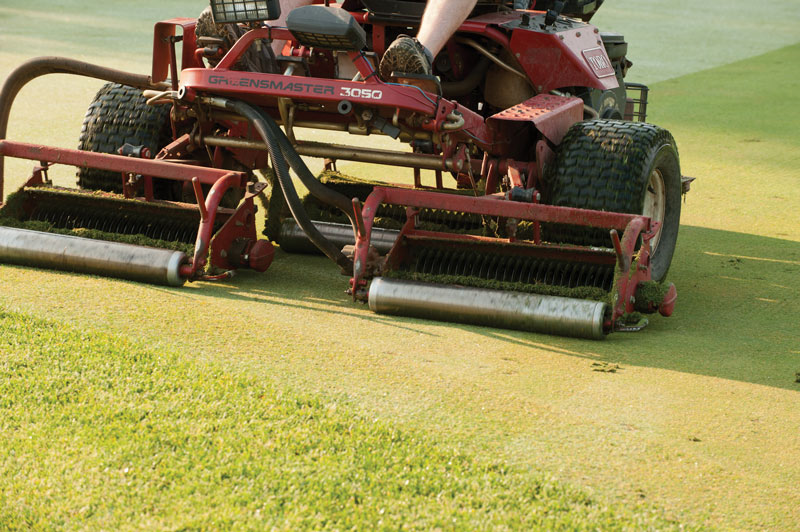
If you can find equipment’s sweet spot for oil change intervals, you’ll save on operating costs while also reducing the amount of waste your facility generates. Photo by Montana Pritchard
Change your oil every 3,000 miles — that was the automotive industry’s edict for decades. Today, improvements in engine technology and synthetic oils have increased that old-school benchmark to a new norm that can range upward of 10,000 miles between oil changes. Recommendations for motor oil changes in turf equipment, however, have largely adhered to a standard 100-hour interval.
In my experience, an average golf course following this guideline will produce at least 55 gallons of waste oil every year. For the 14,288 18-hole-equivalent courses in the United States, that adds up to 785,840 gallons of waste oil annually. What if we’re throwing away perfectly good motor and hydraulic oil just because we’re going by the hour meter instead of checking whether the oil is still within specifications?
Golf course maintenance is site-specific and subject to many variables, with weather, region and even volume of play all factoring into turf management decisions. Just because a turf textbook recommends 4 pounds of nitrogen per year doesn’t mean all superintendents should apply that. So, why the one-size-fits-all recommendation for changing oil?
The easy answer is that equipment manufacturers want their products to succeed, and in order to optimize performance, they’ve established recommendations for oil change intervals that can be safely applied to almost every situation. The other possibility (which makes some people uncomfortable) is that not all oils are the same and not all operating conditions are the same, and users need to address such variables by timing oil changes to meet the wear and conditions of a particular machine.
An equipment manager can turn oil change intervals into a science by using fluid analysis (laboratory testing) to determine when a certain machine’s oil needs to be replaced. Similar to a soil report, a fluid analysis looks at the amount of minerals, additives, wear metals, contaminates, etc., in a sample, and it establishes baselines and thresholds that signal when to change the oil for each sampled piece of equipment. Fluid analysis can even alert you to the presence of wear metals that point to potential equipment failure.
An initial step in implementing a fluid analysis program is to choose which laboratory you’ll work with. Several labs throughout the U.S. perform fluid analysis, but much like soil or water laboratories, not all oil-testing labs provide the same evaluation, and you should investigate the services offered for each sample. Fluid analysis can cost upward of $15 per sample, but it can also be much less in some instances. The price often depends on how extensive the analysis. These labs want your business, and they may offer educational opportunities to help you and your staff gain an understanding of how oil testing can benefit your operation.
Oil testing for every piece of turf equipment can be cost-prohibitive, but with some steps, you can determine each machine’s optimal oil change interval based on fluid analysis of just some of your equipment.
-
Begin testing by selecting one piece of equipment that is typical for an equipment group. Testing poor-performing equipment can give insight into what components might be failing.
- Send in samples taken at suggested change intervals — when oil is close to falling out of specs back up to when it’s operating within specs. Use these to establish the new oil change interval, and continue to test to ensure that interval remains sound.
- Send in a sample from the drum to ensure that the quality of the stock oil matches the oil manufacturer’s specifications, and see how the oil wears at 100, 200 and 300-plus hours.
- Consider using higher-quality synthetic oils to extend intervals and improve equipment performance. Not all high-dollar oils can go the distance; do some side-by-side comparisons to find out which oil works best. Oils may initially meet specifications but lack the additives and wear properties of higher-quality oils. (What about a vegetable/bio oil that’s sensitive to turf but terrible on equipment? The safest oil is one that stays in the equipment, because it does its job protecting components from failure.)
Fluid analysis isn’t a new concept, and it has many applications in big industries such as transportation, construction and manufacturing. These businesses can’t afford to change huge quantities of oil simply because a book or manual says so. They instead rely on fluid analysis to make such decisions. If you can find the sweet spot for oil change intervals, you’ll save on operating costs while also reducing the amount of waste your facility generates. With today’s oils, it may be possible to go 400-plus hours on turf equipment motors, and even a lifetime with hydraulic oils.
Pamela C. Smith, CGCS, is an attorney and the director of agronomy for a large city. She is a 26-year member of GCSAA.